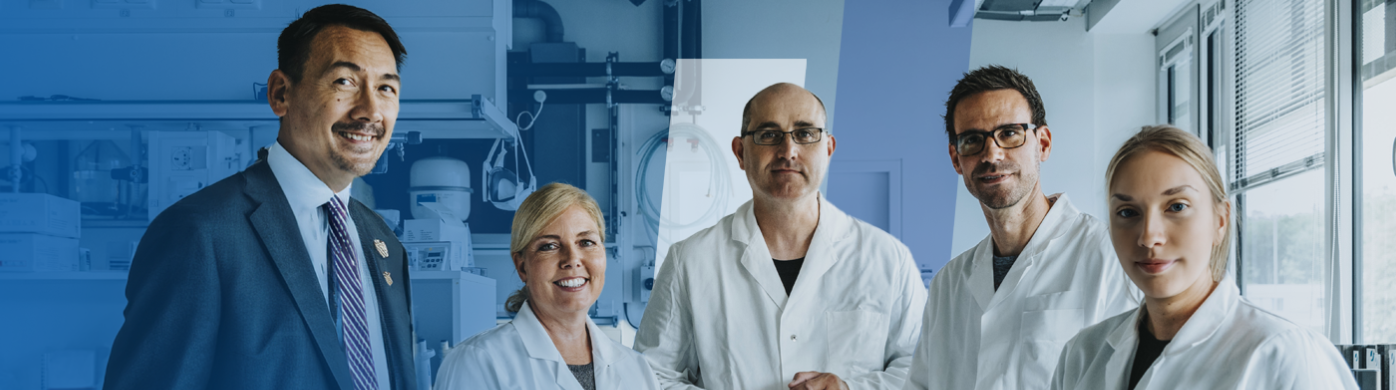
Responsibilities
Location Collegeville, PennsylvaniaUS Job ID REQ-054390Job Responsibilities:
Process Engineering:
- Conduct laboratory experimentation and analytical testing of putative formulations & drug product manufacturing
- Follow administration/delivery approaches for select protein therapeutic assets, including contributing to, the conception & evaluation of conventional & novel product matrices and administration modalities
- Partner closely with the manufacturing groups during process development and technology transfers
- Actively participate with combination drug product assessment and collaborate with device engineering
- Physicochemical and bioanalytical characterization of native and modified biopharma compounds
- Collaborate with the Bioanalytical Sciences group to develop & transfer stability-indicating analytical methods for use in product development
- Oversee release & stability testing; crafting & execution of non-GMP stability protocols to test quality & stability of product formulations
- Engage with the Analytical Technology Transfer and Stability group to craft GMP stability protocols
- Assess resultant data; working closely with internal & external discovery and development support partners as needed
- Develop and implement chemometric process models to support process monitoring and control activities during pilot scale and commercial manufacturing.
Modeling:
- Establish Hybrid/mechanistic process models to accelerate development, increase fundamental understanding, improve risk assessment and deliver more robust processes, products and regulatory filings.
- Implement modelling and simulation directly on key projects to increase fundamental understanding and greatly reduce labor, materials and time required to identify commercial processes.
- Upskill project team members to expand the use of simulation and work with internal and external experts to development /maintain core simulation software platforms.
- Champion integration of new ways of working into existing QbD workflows (e.g. Process Design, Control Strategy Identification, Risk Assessment), regulatory filing strategies and life cycle planning.
- Provide or coordinate training and real-time support to expand the use of chemometrics and mechanistic modeling (simulation) across business modalities.
- Stay current with new modeling techniques through publications, conferences and academic and precompetitive collaborations
- Advocate and comply with GMP requirements for recording experiments and associated data and writing modeling sports including scientific review and data checking.
- Adhere to requirements of Good Manufacturing Practice, Safety, Quality for the Patient and GSK policies and procedures (sites and department).
- Provide critical support outside area of expertise if required to make sure projects meet development timelines.
Leadership:
- Mentor and train staff at client location regarding best-in-class customer support, follow up communication and specific laboratory support skills to drive growth and customer satisfaction
- Collaborate with ServiceManager to drive talent development, overall business performance, and succession planning
- Accountable for all assigned staff administrative duties; including on-boarding, work hour documentation/approval, expense report approval, time-off, etc.
- Work with Service Managerto ensure on-site team is efficiently deployed and has proper training with cross training opportunities defined
- Facilitate team lead meetings, as well as one on ones, performance reviews/evaluations
- Address disciplinary and/or performance problems when necessary in accordance with company policy
- Facilitate interviews for all new hires and ensure successful onboarding
- Identify and/or create necessary SOP's, Work Instructions and documentation to ensure you and your team carry out activities in a consistent and reliable manner.
- Maintain training and compliance in areas of health and safety, security, environmental and operational aspects of daily activities in the working environment
Nothing in this job description restricts management's right to assign or reassign duties and responsibilities of this job at any time
Critical Skills:
- Demonstrated ability to independently design and execute work plans and experimentation to support models development.
- Good interpersonal, organizational and communication skills.
Basic Qualifications:
- PhD degree in Pharmaceutics, Chemometrics, Biology, Chemistry, Chemical Engineering, or related scientific discipline
- 1-3 years of protein formulation and drug delivery development experience
- Master's degree in Pharmaceutics, Chemometrics, Biology, Chemistry, Chemical Engineering, or related scientific discipline
- 5-7 years of similar experience in protein formulation and drug delivery development experience
- Mastery of mainstream chemometric techniques (multivariate classification, calibration, pattern recognition, PCA/PLS) and familiarity with design of experiments concepts and methods.
Preferred Experience:
- Experience with both conventional and alternative biopharmaceutical protein formulation, and drug product development, including the application of DOE and other statistically based experimental design/interpretation approaches.
- Experience with protein product manufacturing processes and development (e.g., solution (vial/PFS), or lyophilization; container/closure assessment & selection), drug delivery (e.g., combination product, device & administration kit) feasibility and compatibility evaluation.
- Experience and understanding of multiple bioanalytical and biophysical assessment techniques for product characterization and product stability evaluation, including HPLC, SDS-PAGE/CGE, SEC, Spectroscopy (UV/VIS, fluorescence, or CD), DSC, particles evaluation by HIAC and/or orthogonal techniques (eg MFI, FlowCam, Archimedes), capillary electrophoresis & chip-based methods, etc.
- Experience in authoring, contributing to, and critical review of successful regulatory submissions; with particular emphasis on late clinical phase submissions, BLA/MAA filings, response to regulatory questions, and pre-approval inspection experience.
- Experience in working with in vivo/ in vitro models to critically assess formulation & delivery modalities
- Experience in drug product manufacturing technology transfer to commercial and/or scale-up of clinical drug product manufacturing capabilities would be beneficial.
- Experience in the use of advanced chemometric methods for process modeling (MSPC, MCR) and 'data wrangling' for signal processing and feature extraction.
- Familiarity with other data driven machine learning methods (SVM, ANN, Bayesian modeling) or the application of hybrid empirical/mechanistic modeling.
- Experience using data analytics and modeling tools for chemical and/or biochemical processes.
- Industrial experience in one or more of the following areas: iii) biopharmaceuticals development; iv) product industrialisation and manufacturing.
- Programming experience using languages such as Matlab, Python, R or C
- Familiarity with Quality by Design concepts, their application and ICH Q8/Q9/Q10 guidelines.
- Experience in the definition of data and informatics requirements for digital platforms supporting modeling.
Working Environment:
- Must be able to work in a laboratory, controlled environments requiring personal protective equipment (e.g., lab coat, safety glasses, etc.) in laboratory.
- Job pace may be fast and job completion demands may be high.
- Must be able to remain in a stationary position more than 25% of the time
- The person needs to occasionally move between labs, corridors, adjoining rooms, and buildings onsite. Frequently operate on instruments, objects, tools or controls, which will require regularly bending, squatting, stretching and reaching in order to perform in a service function.
- Occasionally move or lift up to 25 pounds (potential for occasional lifting of up to 50 pounds).
- Specific vision abilities required by this position include without limitation, the ability to observe details at close range distance vision, color vision, peripheral vision, depth perception, and ability to adjust focus in order to perform the essential service functions of this position.
- Occasionally operates a computer and other office machinery, such as a calculator, copy machine, and computer printer.
- Employee may be required to handle hazardous waste according to local, state, and federal regulations. Duties may include identifying, handling, generating, accumulating, storing and labeling hazardous waste.
- Potential risk to lab-based hazards including but not limited to extreme temperature, biological materials, hazardous chemicals.
- May be required to complete Medical Clearance, Respiratory Protection Training, and Fit Testing to wear a respirator as protection against animal allergens where animals are present in the laboratory environment.
The annualcompensation range for this full-time position is $83,720.00 to $125,320.00. The final base pay offered to the successful candidate will be determined by factors including internal equity, work location, as well as individual qualifications, such as job-related skills, experience, and relevant education or training.